

“Everything under one roof”
Diamond Black was established in 1999 and has been supplying the vinyl record market ever since. We have our own cutting studio and 18 bath galvanics with over 100 years of experience between our engineers. We supply print for vinyl, including sleeves, labels, inserts, stickers and have a whole fulfillment department to cover your needs. We manufacture 7”, 10” & 12” records, black or coloured, as well as marble, splatter, colour-in-colour and A/B effects. We also make picture discs in all three sizes. We like to cover most bases.
We work with DJs, Artists, Record labels, Collectors and more. No job is too small. Enter your specification into our vinyl builder and see how much it will cost you. Alternatively, give us a call or email.
Located just across the road, our sister company PDC Engineering manufactures pressing moulds, pins, bushes, and other essential components for the vinyl production industry. This company is ran by the same people so we always get the parts we need. This close relationship allows for rapid customization and repair of pressing equipment, ensuring minimal downtime and maximum efficiency in our production process. If you’re interested in purchasing from PDC, gives us a call or email.
Everything In-House at Diamond Black - Est 1999
At Diamond Black, we pride ourselves on our comprehensive in-house capabilities that cover almost every aspect of vinyl record production. This unique setup allows us to maintain strict quality control, reduce lead times, and offer a seamless production experience for our clients. Here's an overview of our facilities and services:

Cutting Services
While we do not offer mastering services, our cutting capabilities are top-notch. We require that the audio supplied to us is ready to be cut onto vinyl. Our skilled technicians ensure that each cut is precise and meets the highest standards of audio fidelity.

Vinyl Pressing
Diamond Black boasts its own pressing facilities, equipped with both auto and manual presses. This includes our legacy Toolex Alpha presses, renowned for their durability and quality, and our newly rebuilt presses, increasing our capacity and flexibility. This in-house capability ensures we can meet the demands of any production scale with exceptional quality.

In-House Galvanics Facilities
Our state-of-the-art galvanics department which our engineers have over 60 years experience in handles the electroplating process crucial for creating metal stampers from lacquer masters. With 12 high-speed tanks and 6 pre-plate tanks, we can process both lacquers and Direct Metal Masters (DMMs) efficiently. Our custom-built cooling system enhances efficiency, making us highly proficient in this specialised field.
Packing and Finishing
Our dedicated packing area handles all aspects of fulfilment for the vinyl records. This includes shrink wrapping and labelling, ensuring that every record is ready for retail or distribution. Our attention to detail in the packing process guarantees that the final product not only sounds great but also looks impeccable.
Sister Company: PDC Engineering
Located just across the road, our sister company PDC Engineering manufactures pressing moulds, pins, bushes, and other essential components for the vinyl production industry. This close relationship allows for rapid customization and repair of pressing equipment, ensuring minimal downtime and maximum efficiency in our production process.
Print and Label Services
While we do not produce any printed materials such as labels or sleeves in-house, we maintain strong relationships with several reputable UK printing companies. These partnerships allow us to fulfill all our printing needs, ensuring that the visual aspects of your vinyl records are of the highest quality.
The Benefits of Being Fully In-House
Our extensive in-house capabilities mean that we are not reliant on other companies to make our operations run smoothly. This independence is rare for a UK-based vinyl production company and provides numerous benefits:
- Quality Control: Every step of the production process is closely monitored to ensure the highest standards.
- Reduced Lead Times: With everything managed under one roof, we can expedite the production process, reducing waiting times for our clients.
- Flexibility: Our ability to rapidly adapt to client needs and industry changes sets us apart in the market.
- Reliability: With less dependency on external suppliers, we can consistently meet production deadlines and maintain steady output.
At Diamond Black, our commitment to in-house excellence ensures that we deliver top-quality vinyl records, every time. Our unique setup allows us to offer a level of service and reliability that is unmatched in the UK vinyl production industry.
The process explained
All of these improvements have been conceived and executed by our talented in-house team.

Cutting
Once the audio is mastered, it is sent to a cutting engineer who uses a specialized lathe to cut the audio onto a lacquer disc. The cutting lathe has a heated stylus that etches the sound wave directly into the lacquer, creating a spiral groove from the outer edge to the center of the disc. This groove is a physical representation of the sound wave, with variations in the groove corresponding to different sound frequencies and amplitudes.

Processing
Modernizing Our Manual Presses
In vinyl production, galvanic processing (electroplating) creates the metal stampers used for pressing records. The lacquer master is coated with silver, then electroplated with nickel to form a metal master. From this, a metal mother is made, which can be electroplated again to produce multiple stampers. These stampers are the final tools used to press vinyl records in production. The process ensures durability and accuracy for mass replication.
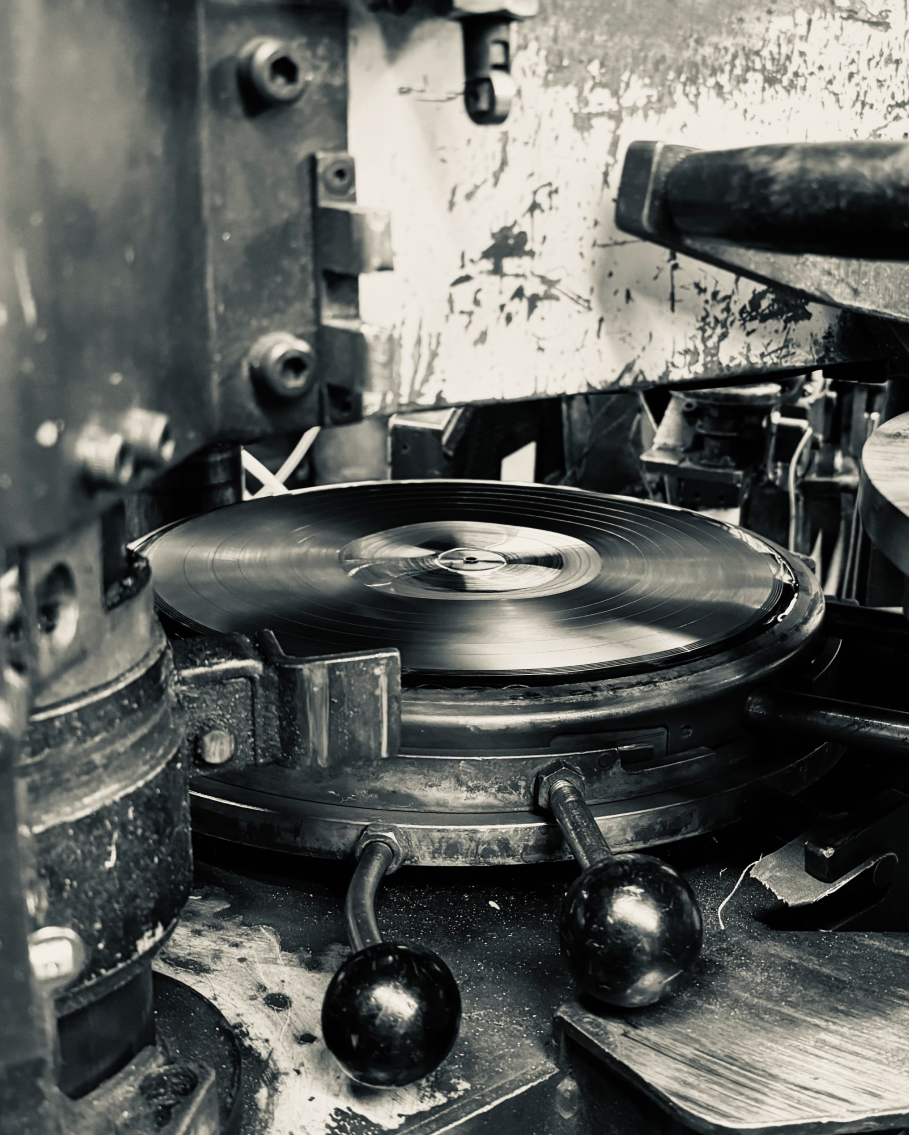
Test pressings
Before we begin the main production run, we create 10 test pressings, commonly referred to as TPs. These test pressings serve as a quality reference to ensure the final product meets our high standards. We will send these TPs to you for approval before we proceed with the full pressing of your records.

Pressing
Our automatic pressing machines extrude the vinyl material into a 'puck' or 'cake.' This puck is placed between two stampers, along with the labels of your choice. The hydraulic press then squeezes everything together while steam melts the vinyl and water cools it. This process takes about 30 seconds. Any excess vinyl around the edges is trimmed off, and the records is left to cool for 24 hours to ensure it remains flat before packing.

Packing
Once the records are cool, they are packed by hand according to your preferences. The most common packing method involves placing the record in a white paper inner sleeve, followed by a 3mm spined outer sleeve, and then shrink-wrapping it. For double albums, a 5mm spined sleeve or a gatefold sleeve, which opens like a book, is required.
For a more cost-effective option that still allows for customization, a 'disco' sleeve can be used. This type of sleeve does not have a spine, eliminating the need for an inner sleeve. Additionally, there are clear plastic inner sleeves available, and Japanese bags can be used instead of shrink wrap. These Japanese bags are resealable, providing excellent protection and convenience.